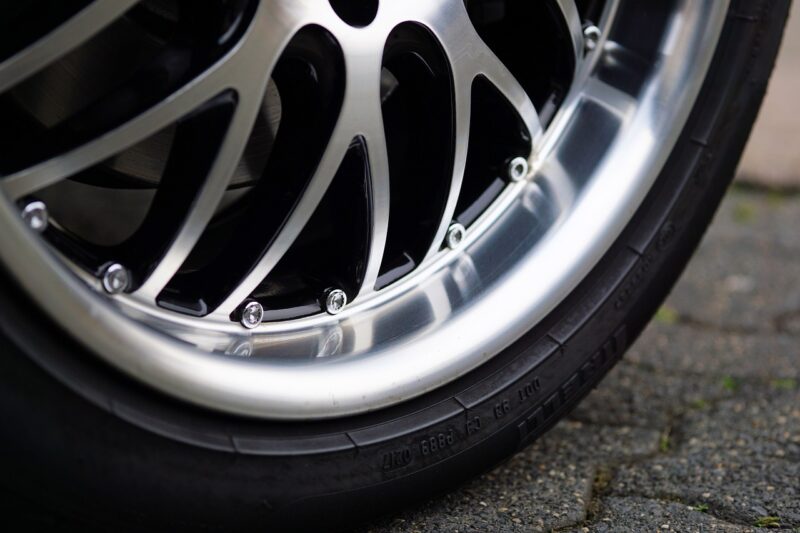
Metals are crucial materials used in countless applications, from construction to aerospace engineering. While pure metals like iron, copper, and aluminum have unique properties, their performance can be significantly enhanced through alloying. Metal alloys combine two or more elements, often enhancing their strength, toughness, and resistance to corrosion. This article explores the reasons why metal alloys are generally stronger than their pure metal counterparts, delving into the science behind this phenomenon.
1. The Basics of Metal Alloys
Alloys are formed by combining a base metal with one or more additional elements. This incorporation can result in various changes in the properties of the base metal, leading to the creation of stronger and more versatile materials. Understanding the structure of alloys is fundamental.
**Types of Alloys:**
– **Ferrous Alloys:** These alloys contain iron and are known for their strength and durability. Common examples include steel, stainless steel, and cast iron.
– **Non-Ferrous Alloys:** These are composed of metals other than iron, such as aluminum alloys, bronze, and brass. They are highly prized for their corrosion resistance and lightweight characteristics.
2. How Alloying Enhances Strength
The strength of metal alloys can often be attributed to several mechanisms that occur at the atomic level. Here are the primary factors that contribute to increased strength:
**a. Solid Solution Strengthening:**
When alloying elements mix with the base metal, they create a solid solution, where the atoms of the alloying elements occupy spaces in the metallic lattice. This disrupts the regular arrangement of atoms, making it harder for dislocations (defects in the crystal structure) to move. As a result, the alloy exhibits higher strength compared to pure metals.
**b. Precipitation Hardening:**
Some alloys undergo precipitation hardening, where tiny particles of a second phase form within the metal matrix. These particles hinder dislocation motion, further enhancing strength. Alloys like aluminum-copper and some high-performance steels utilize this process effectively.
**c. Grain Size Refinement:**
The processes of alloying and subsequent processing can lead to grain size refinement. Smaller grains can enhance strength, as they provide a greater number of boundaries that block dislocation movement. This phenomenon is captured in the Hall-Petch relationship, which states that smaller grain sizes lead to increased material strength.
3. Types of Strength and Toughness in Alloys
Different alloying elements can provide varied types of strength and toughness:
**a. Tensile Strength:**
This refers to the maximum stress an alloy can withstand while being stretched or pulled before failing. Alloys such as high-strength steel exhibit exceptional tensile strengths compared to their pure metal counterparts. This is crucial in applications involving tension, like cables and beams.
**b. Yield Strength:**
The yield strength of an alloy is the stress at which it begins to deform plastically. Steel alloys often have much higher yield strengths than pure iron, ensuring that they can be used in structures that need to withstand heavy loads without deforming permanently.
**c. Toughness:**
Toughness refers to an alloy’s capacity to absorb energy and plastically deform without fracturing. Tough alloys, such as ductile iron, can endure shocks and impacts, making them ideal for applications like automotive components and tools.
4. Corrosion Resistance: A Key Benefit of Alloys
While strength is paramount in many cases, resistance to environmental factors like corrosion is equally critical. Metal alloys often demonstrate superior resistance to corrosion compared to pure metals. This is especially significant in industries exposure to harsh conditions.
**a. Stainless Steel:**
An exemplary corrosion-resistant alloy, stainless steel contains chromium that forms a protective oxide layer, preventing rust and degradation. This property is one reason stainless steel is extensively used in marine applications, kitchenware, and medical devices.
**b. Aluminum Alloys:**
Adding elements like zinc, magnesium, or copper to aluminum enhances its strength significantly and improves its overall resistance to corrosion, ensuring that structures made of aluminum alloys are both lightweight and durable.
5. Real-World Applications of Metal Alloys
Metal alloys are omnipresent across various sectors, reinforcing the importance of understanding their advantages:
**a. Construction:**
Steel alloys are the backbone of modern construction, with structural steel beams providing essential support for buildings and bridges. Their high strength-to-weight ratio enables the construction of towering skyscrapers and expansive bridges.
**b. Aerospace:**
In aerospace engineering, alloys are chosen for their specific strengths-to-weight ratios, corrosion resistance, and fatigue performance. Aluminum-lithium alloys, for example, reduce weight while maintaining strength, contributing to fuel efficiency.
**c. Automotive:**
Automobiles heavily rely on metal alloys for frames, engines, and components. High-strength steels and aluminum alloys enhance performance, durability, and safety, while also improving fuel efficiency through weight reductions.
Conclusion
The objectives of implementing metal alloys—enhanced strength, improved durability, and corrosion resistance—make them vital to several industries. Understanding the role of alloying elements in fortifying the characteristics of metals opens pathways for innovation across engineering and manufacturing.
As technology advances, so too will the development of new alloys designed for specific applications, further emphasizing the ongoing importance of material science in our world. As you consider metal alloys for your next project or application, remember that the ultimate performance often lies not in the metal itself but in the meticulous engineering of its alloys.
With the continued research and innovations in material technology, we can expect to see even more remarkable advancements in the realm of metal alloys that will shape the future of industries worldwide.