How Vinyl Records are Pressed and the Art of the Perfect Groove
November 13, 2024
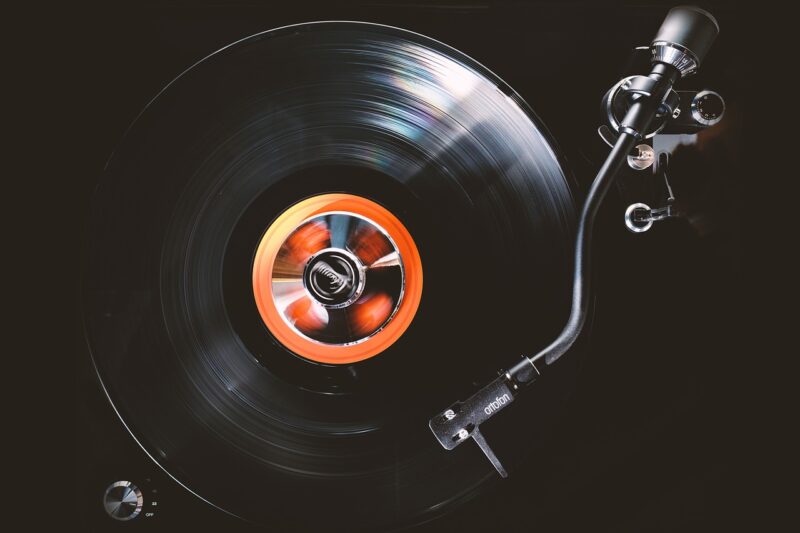
Vinyl records have experienced a remarkable resurgence over the past decade, captivating audiophiles and collectors alike with their rich sound and tactile aesthetic. Beyond the nostalgia associated with records, the craft of vinyl pressing is a fascinating blend of art and science that ensures each groove is a perfect vessel for audio fidelity. In this article, we explore the intricate process of how vinyl records are pressed, the technology behind it, and the artistry involved in creating the perfect groove.
1. The Anatomy of a Vinyl Record
Before we delve into the pressing process, let’s take a moment to understand what a vinyl record is. A vinyl record is made primarily from polyvinyl chloride (PVC) and is designed to hold audio in the form of grooves etched into its surface.
These grooves are a series of undulating patterns that translate sound waves into a physical representation. As the needle of a turntable moves through these grooves, it vibrates, converting the physical movements back into sound. Vinyl records come in various sizes, with the most common being 12-inch LPs (long plays) and 7-inch singles.
2. The Vinyl Pressing Process
The process of pressing vinyl records is an art form that requires precision and expertise. It generally involves the following steps:
Step 1: Mastering
Before a record can be pressed, the audio must be mastered. This involves preparing the final mix by adjusting levels, equalization, and compression to ensure that it sounds the best on vinyl. Mastering for vinyl is different from digital mastering because it requires consideration of how audio translates to the physical medium. The low-end frequencies, for example, need to be well balanced to avoid excessive vibration and distortion.
Step 2: Creating the Master Disc
Once mastering is complete, the audio is transferred to a master disc, typically made of metallic lacquer. This disc is spun on a lathe, where a tiny cutting stylus carves the grooves that will become the record. The depth and shape of the grooves are crucial, as they dictate how the audio will sound when played back.
Step 3: Nickel Plating & Stamper Creation
Next, the master disc undergoes a nickel plating process to create a stamper. The lacquer master is coated with nickel, and the resulting negative is a stamper that contains the grooves to be pressed into the vinyl. This stamper is then used to replicate records, and multiple stampers can be made from a single master.
Step 4: Vinyl Pellets & Heating
For the actual pressing, the raw material—PVC pellets—are heated until they become pliable. This material is then formed into a disk shape, known as a ‘biscuit,’ which is ready for pressing.
Step 5: The Pressing Machine
The heated biscuit is placed between two stampers in a hydraulic pressing machine. The machine applies intense heat and pressure, causing the biscuits to expand and fill the grooves of the stamper. This process creates a record that mirrors the grooves cut into the master disc. Depending on the specifications, this can take anywhere from 20 to 30 seconds.
Step 6: Cooling and Trimming
After pressing, the records are cooled before being trimmed. The excess vinyl around the edges is cut away to ensure a clean finish. If the run is successful, the records are labeled, packaged, and prepared for distribution.
3. The Art of the Perfect Groove
Producing high-quality vinyl records is not just about following a mechanical process; it requires an artistic approach. The shape and depth of the grooves can drastically impact audio quality. Here are some artistic considerations:
- Cutting Techniques: S skilled lathe operator can manipulate the angle, depth, and shape of the grooves while cutting the master disc. Techniques like ‘notching’ the grooves can help prevent distortion and improve fidelity on certain frequencies.
- Groove Spacing: The spacing between grooves must be carefully calculated based on the length and loudness of the tracks. Too close together, the grooves can cause distortion. Therefore, artists and engineers work together to ensure that dinamic tracks can be properly spaced and have room for natural movements.
- Optimal Length: Longer records have the potential for better sound quality, as more grooves allow for broader dynamic range. However, longer running time can sacrifice volume and fidelity. Striking the right balance is essential.
The artistry involved in pressing vinyl records is what elevates them to a cherished medium for many music lovers. Impeccably crafted grooves not only assure high sound quality but also contribute to the overall experience of listening to music on vinyl.
4. The Future of Vinyl Pressing
While vinyl records have seen a resurgence, the future holds both opportunities and challenges. Many pressing plants are struggling to keep up with demand, resulting in longer waiting times for new releases. Innovations in technology, such as direct-to-vinyl cutting, might provide solutions to meet this demand.
Moreover, the growth of independent artists has created new opportunities for smaller presses, enabling unique styles and limited edition runs that cater specifically to niche markets. The art of vinyl pressing continues to evolve, driven by a passion for high-quality sound and artistic expression.
Conclusion
The journey from soundwave to physical vinyl record is a complex process that reflects both technology and artistry. Understanding how vinyl records are pressed and the significance of the perfect groove enriches our appreciation for this timeless medium. As vinyl continues to captivate both old and new generations, the craftsmanship behind it remains vital, ensuring that future listeners enjoy the warm, rich sounds that only a vinyl record can provide. Embracing this iconic medium not only keeps the music alive but also engages with a culture steeped in artistry, creativity, and passion.
To explore more about the vinyl resurgence, or to get tips on collecting and caring for records, dive into the vibrant community that supports this passionate pursuit.